Students construct custom-designed rocket, compete in American Rocketry Challenge
The American Rocketry Challenge is the largest student rocket-building contest in the world. Thousands of contestants from all over the country enroll annually for a chance to represent America in the Paris Air Show and to win thousands in cash prizes. This year, six of the contestants are Mavericks, and their custom-designed, 3D-printed model rocket is stuffed with iceberg lettuce and a chicken egg.
Juniors Bo Farnell, Josh Siegel, Hannah Woodhouse, Vikram Shah, Matthew Perez and Jessie Beck, along with four Energy Institute High School students, have built a rocket out of a cardboard tube that can fly 147 miles per hour. To keep the rocket from burning, they either use a specialized recovery wadding or pieces of lettuce. To assemble it, they used hot glue. It can shoot up 800 feet in less than a minute.
In order to qualify for the contest, each team must launch a raw chicken egg 800 feet high, and their rocket must stay airborne for 40 to 43 seconds. A judge for the National Association of Rocketry will score the rocket, given that it is within the length and weight requirements. In previous years, 101 winning teams have flown to D.C. for the second round to launch their rockets in front of members of the U.S. Congress. To comply with CDC guidelines, this year’s second and final round will be held at several launch sites across the country.
“We use this software called Open Rocket, and we can plug in that we need the rocket to go 800 feet in a certain amount of time,” Shah said. “If we plug in how much the rocket weighs, how many fins there are and the shape of the fins, it can tell us how far the rocket is going to go.”
The team’s rocket consists of a cardboard tube, a 3D-printed nose, four 3D-printed fins and an engine. The group designed the nose and fins themselves, which, according to Siegel, provides them with a significant advantage.
“Most people just buy theirs off of the internet,” he said. “We make our parts in a program called CAD, and then print them out.”
Siegel considers the team’s best asset to be its launch rail. It reaches seven feet tall and holds the rocket at a ninety-degree angle before it takes off.
“The angle at which you launch your rocket is just as important as what the rocket actually looks like,” Siegel said. “We also have some really powerful engines.”
The Aerospace Industries Association and the NAR, the organizations that run the competition, require that the rocket engines are commercially made. But the propulsion section that contains the engine is only one component of the rocket, and equally as important are the propulsion and ejection sections.
“The propulsion section burns and gets the rocket up,” Farnell said. “Then, after the propulsion section has burned, the delay section gives the rocket time to keep going up. After the delay section burns, the ejection charge pushes the cone off and allows the parachute to come out.”
The rocket has gone through many modifications, and the team is currently on their fourth design. The first model had a tendency to launch sideways; the second model once caught fire.
“For our first twenty launches, our rockets just blew up,” Perez said. “But the first time we got to see it go up, it really lightened our spirits. We’re not just working; we’re having fun.”
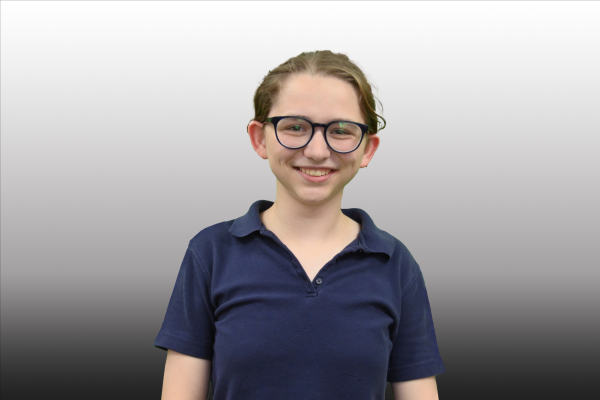
Annie Jones ('24) joined The Review in 2020 as a freshman. She has four younger siblings and considers herself the wunderkind of shenaniganery.